Digital Twins: Revolutionising Product Design and Maintenance in Industry 4.0
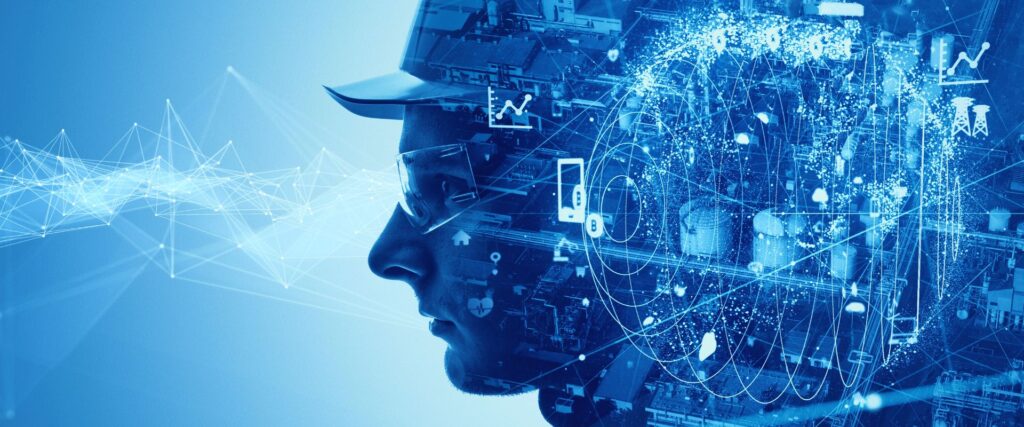
The Fourth Industrial Revolution, or Industry 4.0, has been reshaping the way businesses operate by leveraging advanced technologies such as artificial intelligence, the Internet of Things, and automation. One such innovation, digital twins, is poised to revolutionise product design and maintenance across various industries. In this blog post, we will explore the concept of digital twins, their role in product design and maintenance, challenges and limitations, and future trends and opportunities.
Before we explore the reasons and details behind digital twins, let’s briefly understand them in simple terms.
What are Digital Twins?
A digital twin is a virtual replica of a physical product, system, or process that can be used for analysis, simulation, and optimization. It consists of three key components: the physical product, the virtual model, and the data connection between the two. By creating a digital twin, businesses can gain valuable insights into their products’ performance and identify areas for improvement. Industries such as aerospace, automotive, manufacturing, and energy already benefit from digital twin technology.
The Role of Digital Twins in Product Design
A. Enhancing product design through virtual prototyping
- Reduced time-to-market: Digital twins enable companies to test and iterate their designs virtually, reducing the need for physical prototypes and shortening the overall product development cycle.
- Cost savings: Businesses can avoid costly rework and modifications later by identifying design flaws and inefficiencies early in the process.
- Improved design accuracy: Digital twins provide precise and accurate simulations, allowing for better-informed design decisions and enhanced product quality.
B. Utilising simulations for performance optimisation
- Predicting product behaviour under different conditions: Digital twins can simulate various operating conditions, helping businesses optimise their designs for specific environments and use cases.
- Identifying potential design flaws early on: By testing the virtual model, companies can uncover weaknesses or vulnerabilities in their designs and address them proactively.
- Optimising design for sustainability and efficiency: Digital twins can analyse a product’s energy consumption, emissions, and waste generation, enabling businesses to choose the eco-friendly design.
The Role of Digital Twins in Product Maintenance
A. Real-time monitoring and predictive maintenance
- Minimising downtime and repair costs: By monitoring the performance of a physical product in real time, digital twins can predict potential failures and facilitate timely maintenance interventions.
- Extending product lifespan: Regular maintenance guided by digital twin insights can extend the operational life of products, improving return on investment.
- Improving overall equipment effectiveness (OEE): Predictive maintenance enabled by digital twins can lead to higher equipment availability, performance, and product quality.
B. Remote diagnostics and support
- Faster response to issues: Digital twins can help technicians diagnose issues remotely, reducing the time needed to identify and resolve problems.
- Reducing the need for on-site maintenance visits: Remote diagnostics can minimise the frequency of on-site maintenance visits, saving time and resources.
- Enhanced customer satisfaction: Faster issue resolution and proactive maintenance can lead to higher customer satisfaction and stronger business relationships.
Challenges and Limitations of Digital Twins
- Data privacy and security concerns: Ensuring the privacy and security of sensitive data used in digital twin models is paramount to protecting intellectual property and maintaining customer trust.
- High initial investment and implementation costs: Developing and deploying digital twin technology can be resource-intensive, requiring specialised skills and infrastructure.
- Integration with existing systems and processes: Integrating digital twins with legacy systems and methods may require significant effort and change management.
- Ensuring accurate digital twin models: Maintaining the accuracy and fidelity of digital twin models is crucial for obtaining reliable insights and predictions.
Future Trends and Opportunities for Digital Twins
- Increasing adoption across various industries: As digital twin technology matures and becomes more accessible, we can expect its adoption to expand across a broader range of industries, including healthcare, retail, and construction.
- Integration with other Industry 4.0 technologies: Digital twins can be integrated with other cutting-edge technologies such as AI, IoT, and blockchain to unlock even more significant potential for optimisation and innovation.
- Potential for continuous improvement and innovation: The insights and learnings from digital twins can help businesses identify new opportunities for growth and development, fostering a culture of constant improvement and innovation.
Digital twins offer immense potential to revolutionise product design and maintenance in the era of Industry 4.0. By leveraging virtual models and real-time data, businesses can optimise their designs, reduce time-to-market, minimise downtime, and improve customer satisfaction.
While we know that challenges such as data privacy, high implementation costs, and integration with existing systems remain faithful, the benefits of digital twin technology make it an essential tool for businesses looking to stay competitive and relevant in the rapidly evolving industrial landscape.
As adoption continues to grow, digital twins will undoubtedly play a critical role in shaping the future of industry and commerce. If you are a business owner and want to understand better the benefits of digital transformation and digital twin technology for your business, feel free to get in touch with us. Our experts will be happy to assist you.